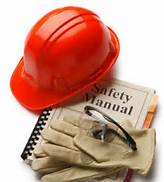
Management commitment
- A clearly established policy for worker safety and health protection that is communicated to all employees.
- Supervisors are held accountable for safety and health as part of their job
- Your company commits adequate resources to workplace safety and health, including staff, training, and equipment.
- Management sets the example of safe and healthful behavior.
- A hazard assessment process
A hazard assessment process can help your company avoid and control risks. Your safety program should include:
An annual comprehensive safety and health program audit, and regular reviews by people qualified to recognize existing hazards and potentially significant risks. This can be done by in-house staff, or by a third-party safety professional.
A reliable procedure that allows employees to report possibly hazardous conditions without fear of reprisal and to receive appropriate and timely responses.
Ongoing monitoring and maintenance of equipment to prevent it from becoming hazardous.
Prompt investigation of accidents, near-misses, and incidents of injury or illness to identify causes and corrective actions.
Safety Rules and Work Procedures
Your safety program should include safety plans, rules, and work procedures for specific operations at your company.
- The rules should be thoroughly understood by supervisors and employees
- The rules should include enforcement procedures, such as disciplinary action or reorientation, that are universally recognized and applied.
- The plan should establish procedures for response to emergencies requiring personal protective equipment, first aid, medical care, or emergency evacuation, with emergency telephone numbers and exit routes visible to all employees, and provide training and drills as needed.
Safety Training
Your company's training program should ensure that supervisors understand the hazards associated with a job, their potential effects on their workers, and their role in ensuring that employees follow the rules, procedures, and work practices for controlling exposure to hazards. It should also make sure that employees understand hazards and safe work procedures. And lastly, where personal protective equipment is required, employees understand the requirement, the reasons for it, the limitations of the equipment, and how to maintain and use it properly.
Safety Performance Tracking and Improvement
The best safety programs include record-keeping and tracking of key leading safety indicators to measure and continuously improve their safety performance.